Benefits of applying CFD simulation in chemical plant design
June 10, 2023 - Reading time: 4 minutes
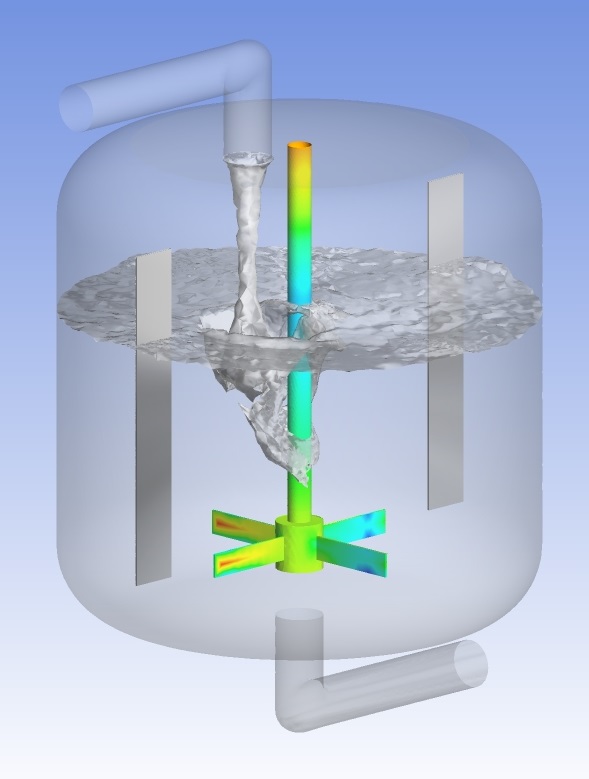
CFD Simulation of a Continuous Stirred Tank Reactor (CSTR) @ Copyright Jimmy Lea
Computational fluid dynamics (CFD) simulations are widely used in chemical plant design to analyze and optimize various aspects of the process, including fluid flow, heat transfer, mixing and reaction kinetics.
Below are several some specific applications of CFD simulation in chemical plant design, namely:
- Flow Analysis: CFD simulations are employed to study fluid flow patterns within different components of the chemical plant, such as pipes, reactors, and heat exchangers. This helps in identifying potential flow disruptions, pressure drops, or areas of recirculation, thus allowing engineers to optimize the design for efficient fluid distribution.
- Heat Transfer Analysis: CFD can be used to investigate heat transfer mechanisms, such as conduction, convection, and radiation, within equipment like heat exchangers and furnaces. It enables engineers to assess temperature distribution, identify hotspots and optimize cooling strategies for enhanced energy efficiency and process safety.
- Mixing and Reaction Analysis: CFD simulations are employed to assess mixing efficiency and reaction kinetics within reactors and mixing vessels. This helps in optimizing the design parameters such as impeller configuration, flow rates and reactor geometry to achieve desired product quality, minimize reaction time and maximize yield.
- Fluid-Particle Interaction: CFD can simulate the behavior of solid particles or droplets in fluid flow, which is relevant in processes like crystallization, spray drying, and fluidized bed reactors. By studying particle trajectories, residence times, and collision patterns, engineers can optimize equipment design and operational parameters to enhance particle-fluid interaction and process performance.
- Ventilation and Air Quality: CFD can analyze the dispersion of pollutants, gases or dust within a chemical plant, aiding in the design of efficient ventilation systems and evaluating worker safety measures. This enables engineers to identify potential exposure risks, optimize exhaust systems and ensure compliance with occupational health and environmental regulations.
- Scale-up and Process Optimization: CFD simulations can be used to scale up processes from lab-scale to industrial-scale by simulating the fluid dynamics and heat transfer in larger equipment. This allows engineers to predict and mitigate potential issues that may arise during scale-up, thereby reducing costs and improving the efficiency of the plant.
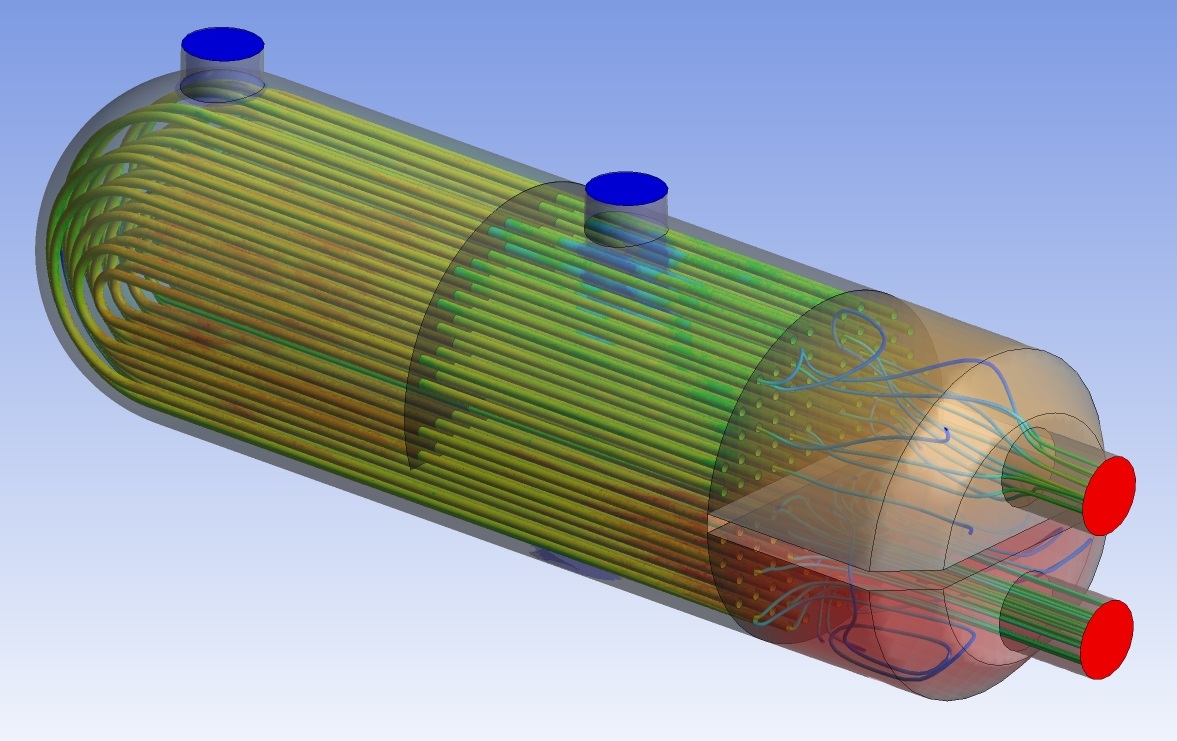
CFD Simulation of a Shell-and-Tube Heat Exchanger @ Copyright Jimmy Lea
The benefits of employing CFD simulations in chemical plant design are:
- Cost and Time Savings: CFD simulations allow engineers to virtually test and optimize different design options before physical construction. This reduces the need for expensive prototypes and physical testing, leading to significant cost and time savings in the design process.
- Enhanced Design Understanding: CFD provides detailed insights into the fluid flow patterns, heat transfer mechanisms, and reaction kinetics within the plant equipment. This understanding helps engineers identify potential bottlenecks, areas of inefficiency, and safety risks, allowing them to make informed design decisions and optimize plant performance.
- Process Optimization: By simulating different operational scenarios, CFD enables engineers to identify optimal process conditions, such as flow rates, temperature profiles, and reaction parameters. This optimization can lead to improved product quality, increased yield, energy savings and reduced environmental impact.
- Safety and Risk Assessment: CFD simulations assist in evaluating safety aspects within the plant by predicting and visualizing hazardous situations, such as gas leaks, dispersion of toxic substances or equipment failures. This allows engineers to implement appropriate safety measures, design effective ventilation systems and ensure compliance with regulatory standards.
- Troubleshooting and Problem Solving: CFD simulations can assist in troubleshooting existing plant issues by analyzing flow disruptions, temperature imbalances or poor mixing. Engineers can identify the root causes of problems and propose design modifications or operational changes to rectify them, thus improving plant reliability and efficiency.
- Design Flexibility and Innovation: CFD simulations provide engineers with the flexibility to explore innovative chemical plant conceptual designs and evaluate their feasibility. It allows for rapid iteration and optimization of design ideas, fostering innovation and pushing the boundaries of process efficiency and performance.
- Environmental Sustainability: CFD simulations enable engineers to assess and minimize the environmental impact of chemical plant operations. By optimizing energy consumption, reducing emissions, improving process efficiency, CFD contributes to sustainable design practices and helps meet environmental goals.
- Regulatory Compliance: CFD simulations assist in ensuring regulatory compliance by predicting and evaluating factors such as pollutant dispersion, safety measures and environmental impact. This helps in designing plants that adhere to local and international regulations, avoiding costly penalties and ensuring a safe operating environment.
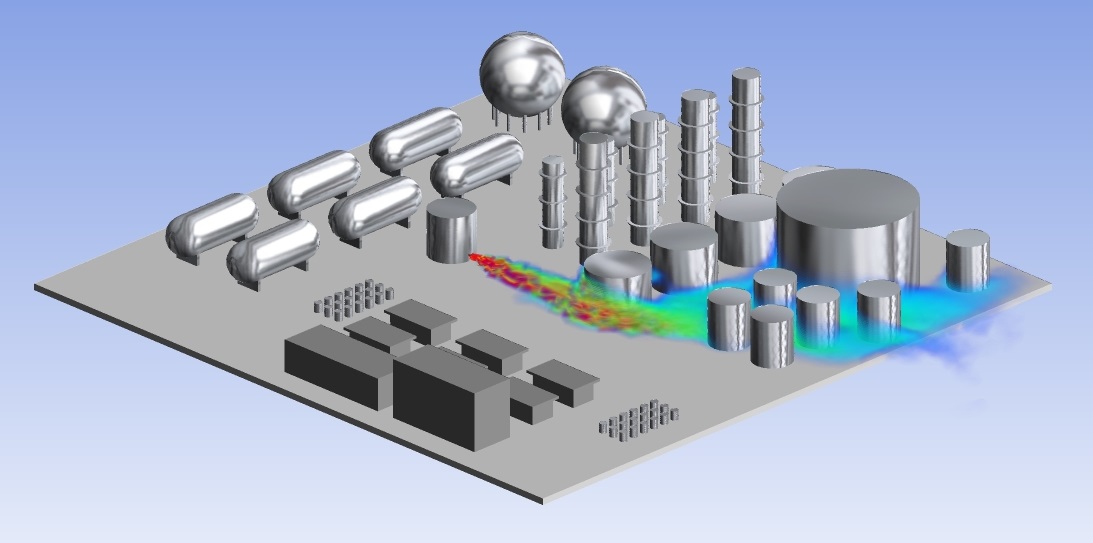
CFD Simulation of Gas Leakage at a Chemical Plant @ Copyright Jimmy Lea
As a chemical process plant consultants, we have been applying CFD simulations in chemical plant design which offered our clients a wide range of benefits, including cost savings, improved understanding of processes, enhanced safety, process optimization, and the ability to explore many innovative process design concepts. It is a valuable tool that empowers our clients to make informed decisions, reduce risks and achieve efficient and sustainable plant operations.
Jimmy Lea P/L
Engineering & Simulation Consultants
Category: [Chemistry]